On-site NDT stiffness assessment and defect detection for composite materials
SINTEG Systems gives composite quality control and manufacturing teams instant insights in material defects and stiffness properties – without lab testing or part destruction
OUR PARTNERS
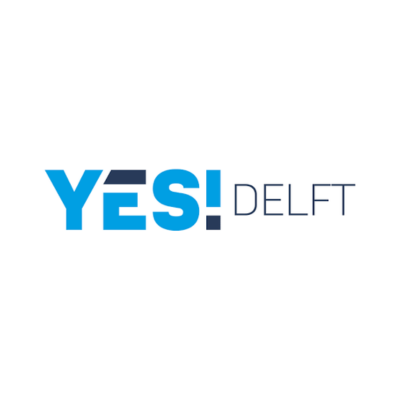
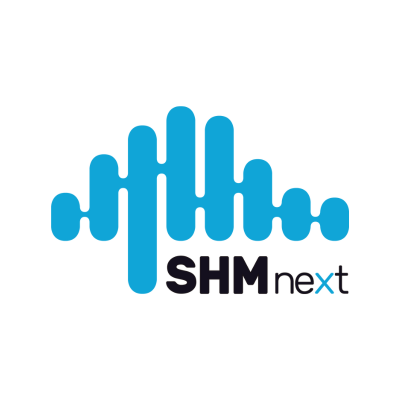

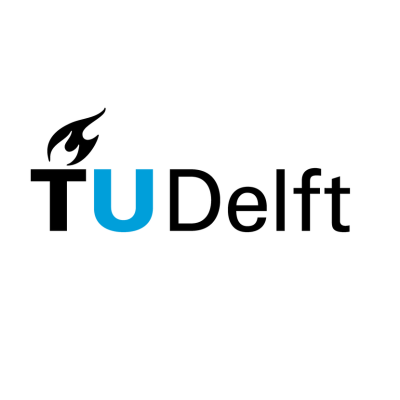
Why we exist
Traditional NDT methods for composite materials are slow, expensive, and limited in what they reveal
Composite materials are at the core of modern engineering, offering unmatched strength-to-weight ratios, durability, and design flexibilities. However, ensuring their structural integrity remains a challenge. Traditional non-destructive testing (NDT) methods are often slow, expensive, and limited in what they reveal, leading to low product reliability, excessive safety factors, and increased production costs.
At SINTEG Systems, we are redefining composite material inspection by offering a real-time, on-site integrity assessment technology to improve product efficiency while meeting strict regulatory demands. Our goal is to support safe, sustainable, and reliable use of composites across all existing and emerging industries.
Call for collaboration
We are currently in the validation phase, working with key industry players to refine our technology. We are actively looking for manufacturing partners and early adopters who want to shape the future of composite NDT with us.
our solution
A compact ultrasonic NDT system that analyses both defects and material stiffness — on-site, in real time
We believe that composite NDT should be smarter, more efficient, and more accessible. With our innovative ultrasound-based inspection technology, manufacturers can move beyond simple pass/fail inspections. SINTEG provides a quantifiable assessment of material integrity, ensuring product reliability and extending component lifecycles.
Our solutions are designed to be cost-effective, scalable, and user-friendly, eliminating complex testing procedures through ML-driven stiffness analysis and automated defect localisation.
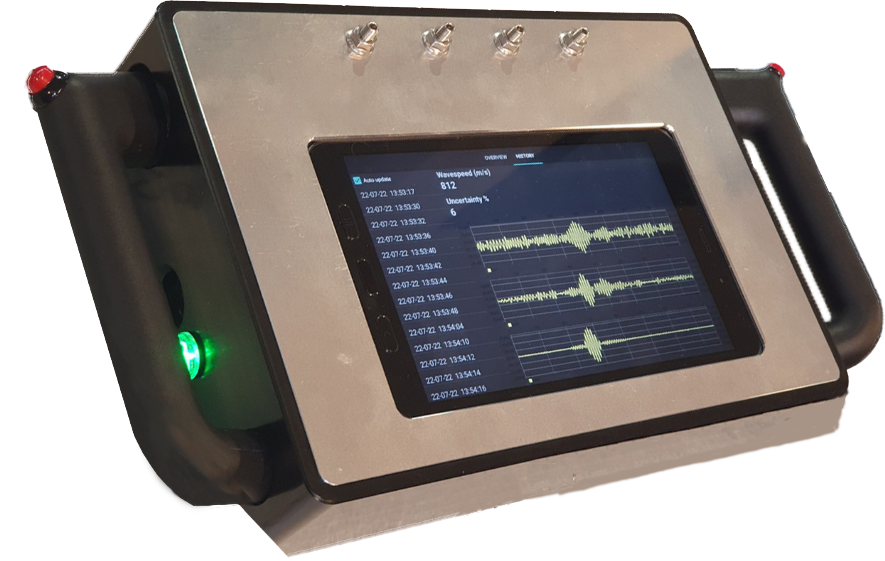
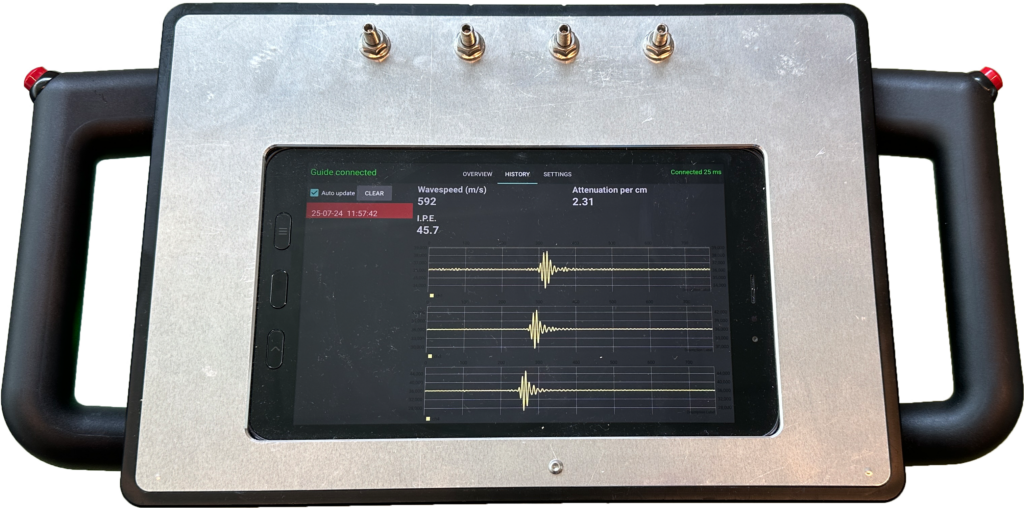
Quantitative stiffness analysis
Our innovative algorithm reveals undesired stiffness variations after manufacturing and monitors their development during lifetime
Rapid inspection
Large areas can be quickly assessed for quality control and in-service checks, reducing inspection time and increasing efficiency
Easy-to-use
No coupling agent is needed, simplifying the process of post-manufacturing quality control and in-service inspection
On-site inspection
A wireless, portable system that works in any location, from existing production lines to in-service inspections
ML-driven analysis
Automated data processing and result interpretation makes our system usable by any level of expertise while eliminating human errors
Compatible with all composites
Adaptable sensor design makes our system suitable for various composite materials and structures.
Key benefits of SINTEG Systems
Eliminate excessive safety factors
Our quantitative inspection method reveals undesired stiffness variations across the composite structure. The intuitive analysis supports improvements in structural design and production procedures, paving the way for reduced safety factors and structural weight
Minimize inspection costs
The efficient design of our system allows quality control and inspection procedures to be performed by any person, regardless of expertise, with minimal training. The portable, non-intrusive system seamlessly integrates into production lines for process control or dedicated inspection workflows — without causing delays or downtimes
Increase quality assurance
The ML-based data analysis and result interpretations eliminate the chance of human errors. The automated evaluation process ensures consistent, objective assessments, enhancing structural reliability while ensuring regulatory compliance.
Maximize structural lifetime
Detecting production-induced defects and stiffness variations, combined with monitoring structural integrity during service, ensures optimal performance and extends the structure’s lifetime.
our industries
Our solutions are versitale and scalable, supporting all composite industries
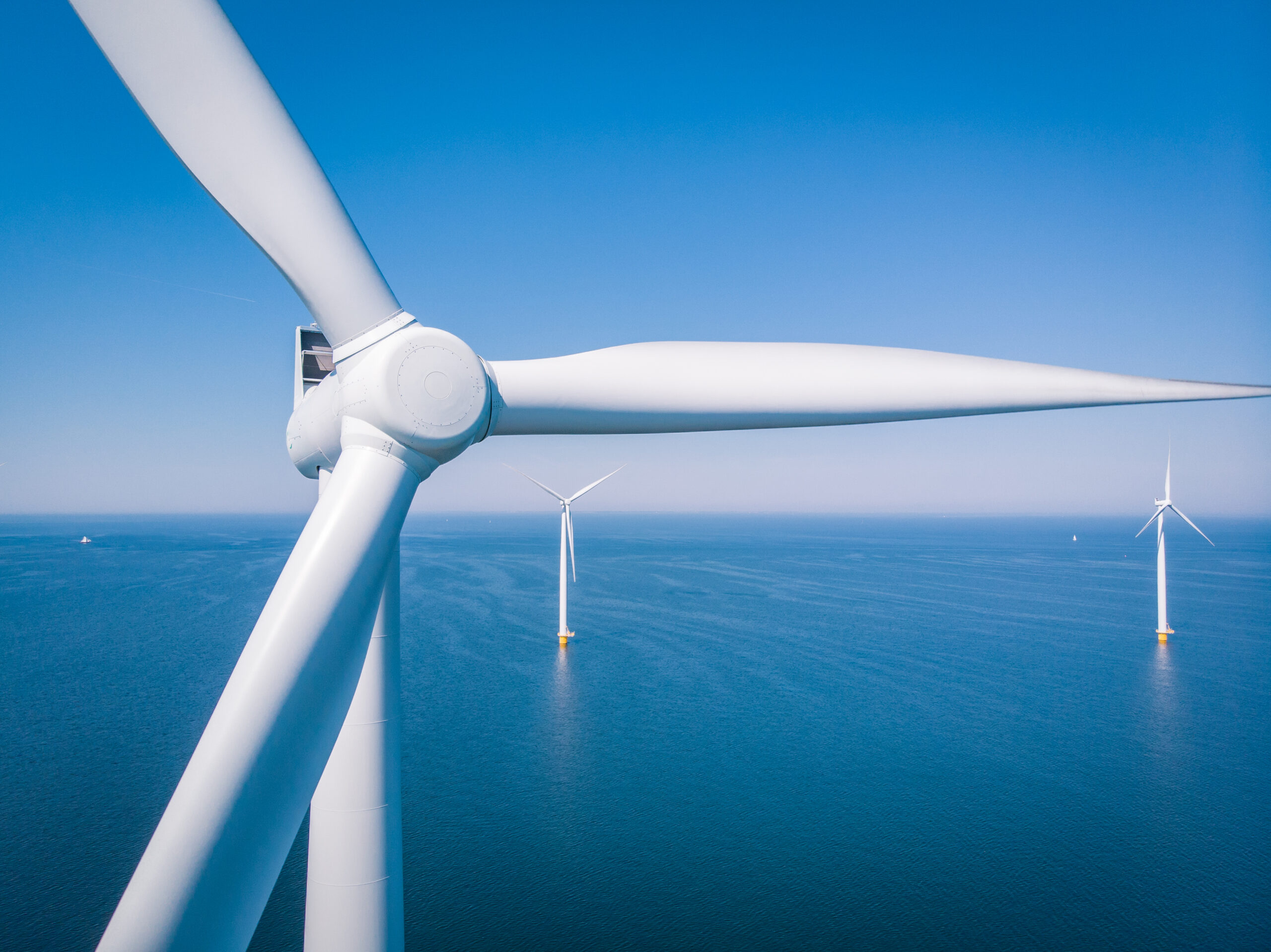
Renewables
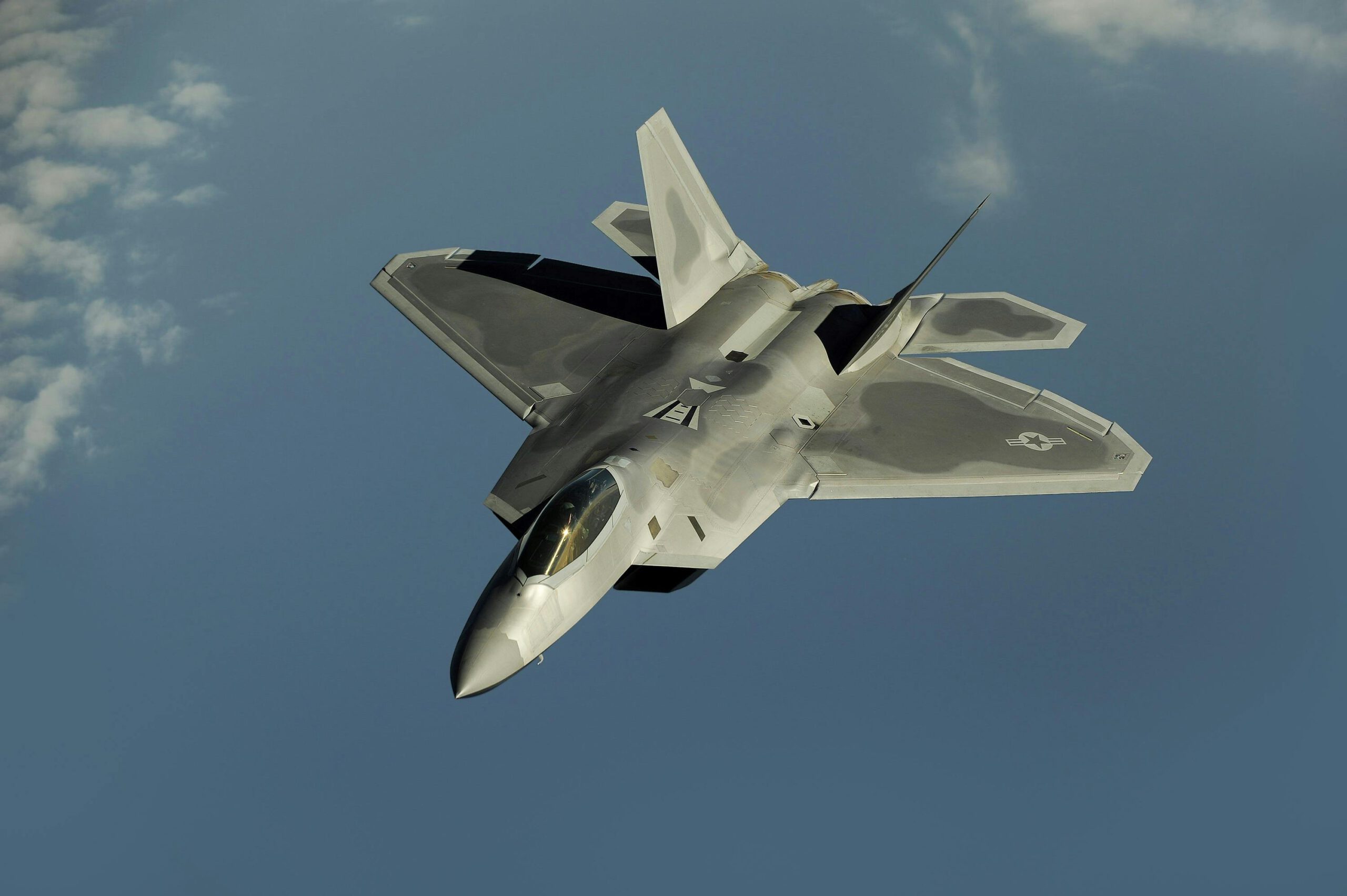
Defence
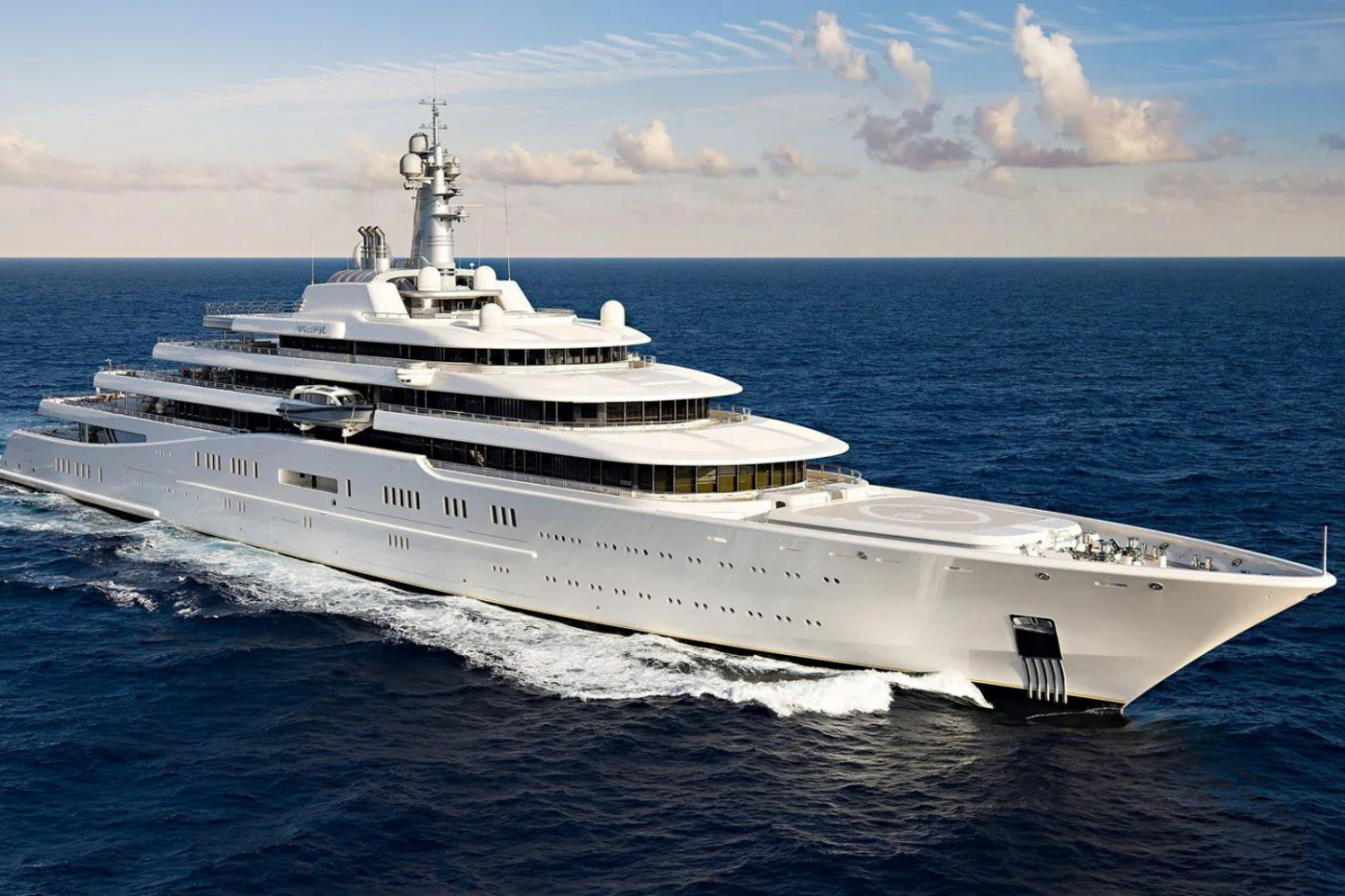
Maritime
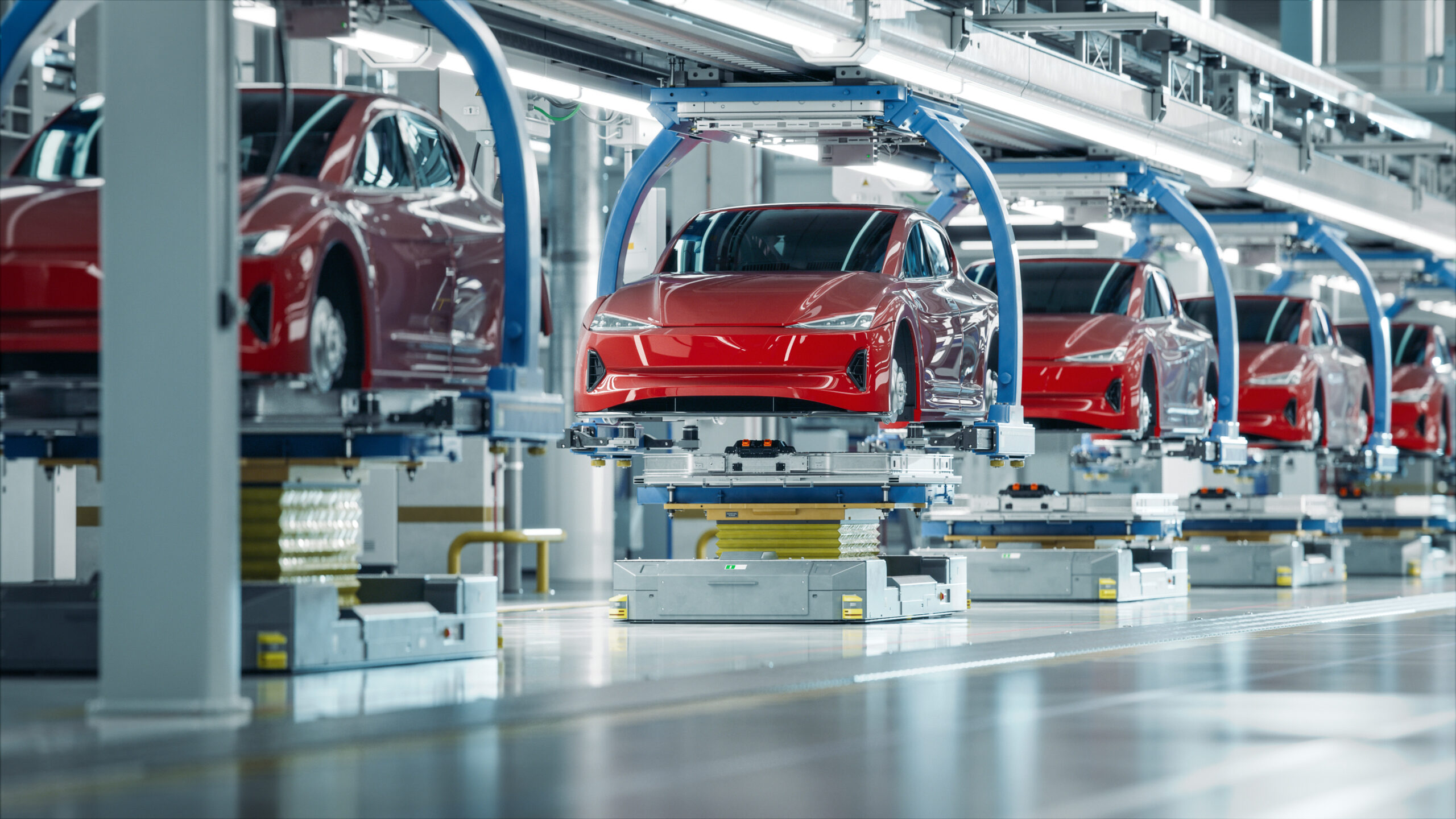
AUTOMOTIVE
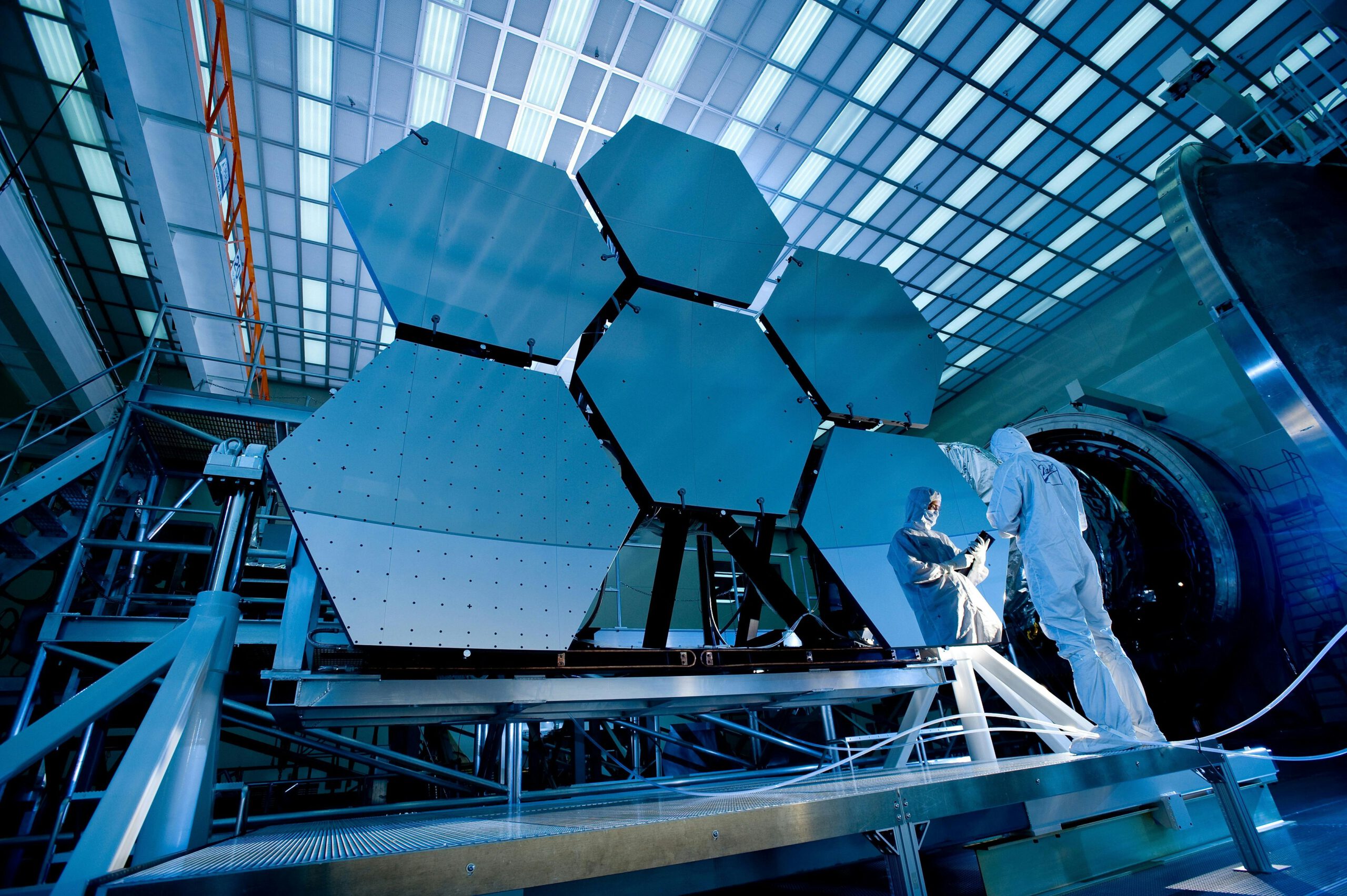
Space
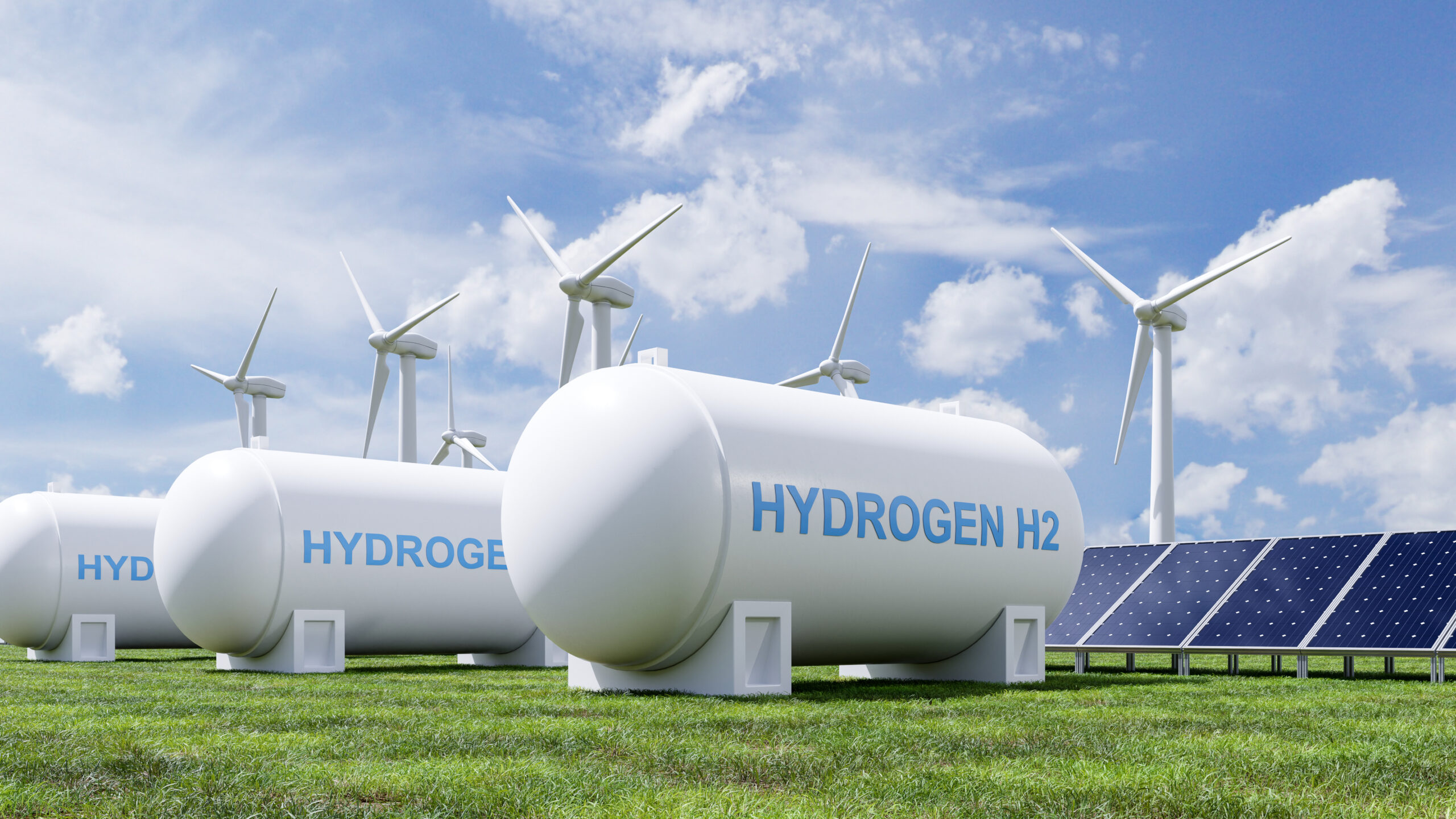
hydrogen storage

aerospace
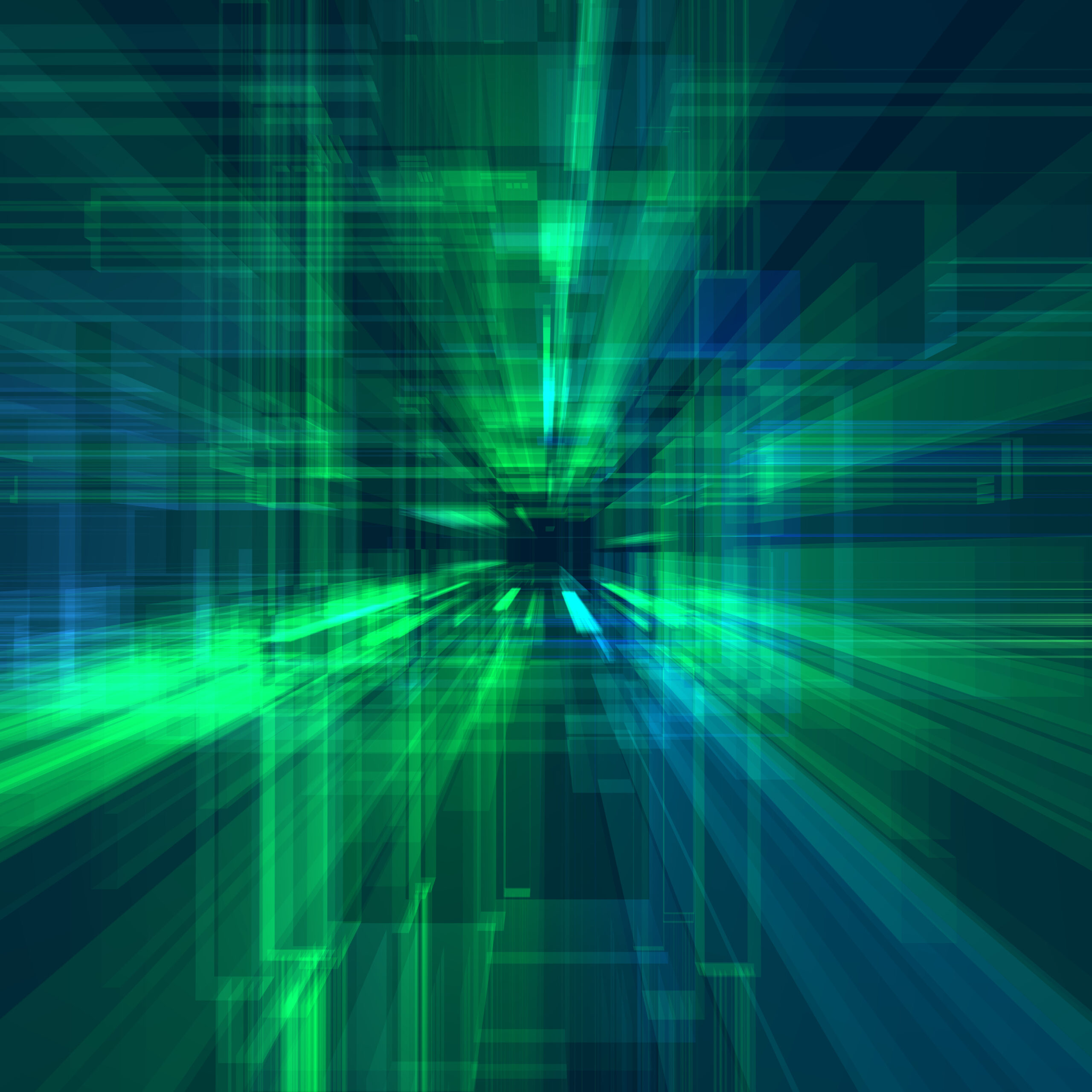
emerging technologies
NEWS
News and Articles
-
SINTEG Systems joins CompositesNL
.
In june, SINTEG Systems officially joined CompositesNL, the leading industry association for the Dutch composites sector. As part of our introduction to the community, we had the opportunity to present…